Old Foundations, New Challenges: Comparing Legacy Coreboard Mills with Modern Builds
- JPT Team
- May 28
- 4 min read
Coreboard—the essential material used to make cardboard tubes and paper cores—is the backbone of many industrial and packaging applications. At Just Paper Tubes (JPT), we source coreboard globally to ensure the best mix of performance, value, and reliability. But one factor often overlooked is the difference between mills built in the mid-20th century and those constructed from the ground up in the last decade.
Many mills in operation today were originally commissioned 60 to 80 years ago. These legacy facilities have been maintained, refurbished, and upgraded over time—but they still sit on old foundations, with key design choices made in a very different industrial age. In contrast, newly built mills are conceived for today’s world: high-efficiency, digitally connected, and environmentally conscious.
This article explores the practical and technical differences between the two—and why it matters when you’re selecting coreboard for high-quality cardboard tubes and paper cores.
1. The Limits of Retrofits: What Legacy Mills Can (and Can’t) Do
Many mid-20th century mills were built to very different standards: narrow machine widths, slower speeds, steam-based heating, and open gearing. Over the decades, these mills have been upgraded—new headboxes, updated drying sections, improved process controls—but they still inherit limitations from their original architecture.
Even with modern touches, a 70-year-old mill may struggle to match the uniformity, speed, or scale of a brand-new facility. Ceiling height, footprint, and outdated substructures can limit the size and efficiency of newer machinery.
At JPT, we work with some legacy mills that produce excellent coreboard—but we also know where their constraints lie. Understanding the difference is key to ensuring consistency and performance for our customers’ paper cores and cardboard tubes.
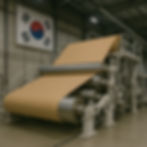
2. Modern Mills: Designed for Today’s Demands
A mill built in the last 10 years is designed with high performance in mind from day one. These facilities often feature:
Wider machines (up to 4.5 metres)
Speeds exceeding 1000 m/min
Fully enclosed systems for dust control
Sophisticated quality control (QCS) and distributed control systems (DCS)
Integrated energy and water recovery systems
These capabilities allow for extremely consistent GSM, moisture control, and bonding—factors that directly affect how coreboard behaves in converting and final use.
When Just Paper Tubes sources from these modern mills, we often see reduced wastage on our converting lines, fewer crush failures, and improved runnability—especially on longer production runs.
3. Energy and Environmental Efficiency
Legacy mills were never designed with environmental performance in mind. While many have added biomass boilers, water treatment, or heat recovery units, these are often bolted onto inefficient base systems. By contrast, modern mills integrate sustainability from the ground up—often reducing energy usage per tonne of board by 30–50% compared to older plants.
Newer mills also tend to have lower Scope 1 and Scope 2 emissions, better water recycling systems, and are built to meet global ESG expectations. For companies seeking lower-carbon packaging solutions, this matters.
At JPT, sourcing from modern mills helps us support customers aiming to decarbonise their supply chains without compromising on performance.

4. Raw Material Handling: Better Cleaning, Better Board
Older mills using recycled fibre often have retrofit cleaning systems that aren’t fully optimised. This can result in fibre bundles, specks, or variability in board stiffness. Modern mills, however, are designed to process 100% recycled content efficiently, with multi-stage cleaning, flotation deinking, and fibre recovery loops integrated from the outset.
This translates into cleaner board, improved reel formation, and less dust—three things our team at JPT always considers when selecting coreboard suppliers.
5. Automation and Downtime
Modern mills are highly automated, with predictive maintenance, real-time monitoring, and advanced diagnostics. This leads to more consistent uptime and fewer surprises. In older mills, despite best efforts, unplanned outages and variable output still occur more frequently—especially when older mechanical components interact with newer control systems.
For JPT, reliability of supply is crucial. That’s why we maintain a balanced global supply chain, combining the best legacy mills with modern facilities to de-risk against interruptions and price volatility.
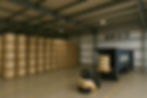
6. Traceability and Transparency
Traceability from legacy mills is often paper-based or semi-digital, making it harder to track batches from raw fibre to final product. Modern mills offer full digital traceability—from pulp origin to board roll—helping with both regulatory compliance and quality assurance.
At Just Paper Tubes, this data allows us to respond quickly to customer queries and ensure our products meet the required specifications every time.
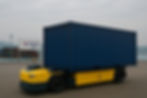
7. Does Old Always Mean Worse? Not Always.
It's important to say: not all old mills are outdated. Some have invested heavily and operate with near-modern efficiency. Others produce board with qualities that suit niche applications—for instance, slightly higher bulk or specific tactile finishes.
That’s why JPT doesn’t write off older mills. Instead, we evaluate each mill on its performance, investment cycle, and output consistency—not just its commissioning date.
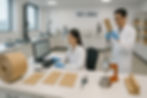
Final Thoughts: Why It Matters to You
Whether you’re buying paper cores for carpet, film, textiles, or mailing tubes, the quality of the coreboard inside matters. Variability, weakness, or dust can translate into lost time and higher costs.
At Just Paper Tubes, we source globally from both established and new-generation mills. What matters to us—and to you—is performance. That’s why we continually assess the technical capability, environmental footprint, and reliability of our supply partners.
So when you choose JPT, you’re not just getting a cardboard tube. You’re getting a product made from the best coreboard the world has to offer—selected by experts, backed by data, and delivered with precision.